In recent years, UV LED curing technology has attracted worldwide attention. In many applications, UV LED light source has been gradually replaced by traditional mercury light source. UV LED is a solid state semiconductor light source. Compared with the traditional UV mercury lamp, it is more environmentally friendly, efficient and has low energy consumption. It is a green industrial technology facing sustainable development.
Compared with traditional UV mercury lamp, UV LED curing system has the following advantages:
Green environmental protection: UV LED does not contain mercury, does not produce ozone, does not need to meet the standard of emissions and waste treatment additional expenses;
Improve production efficiency: instant switch, no need for startup preheating and shutdown cooling; Low failure rate, maintenance time reduced by more than 95%, greatly improve the opening rate of equipment; High UV auxiliary intensity, printing speed can be increased by more than 80%.
Energy saving: lower operating power consumption relative to mercury lamp by more than 70% and standby power consumption relative to mercury lamp by more than 95%;
Improve printing quality: UV LED curing light source light output stability, uniform light spot, can effectively improve the curing quality and uniformity; The peak width of the traditional UV mercury lamp curing machine is uneven and the light spot is decreasing around.
Save a lot of maintenance cost and time: UV LED equipment has few consumables that need to be replaced regularly, mercury lamp needs to be replaced regularly, reflector and other components; UV LED equipment is easy to maintain and the maintenance cost is more than 90% lower than that of mercury lamp.
With the development of The Times and the needs of customers, the printing industry is facing new challenges. The market requires printing product suppliers to adapt to small quantity and variety of orders, faster delivery speed, a variety of printing media, better printing quality and performance forms, while facing fierce price competition. This requires product suppliers to improve product quality, production efficiency and printing conversion efficiency, while maintaining high price competitiveness. The technical advantages of UV LED curing system have been recognized and accepted by more and more users, but the variety of UV LED curing lamps on the market is diverse, and the quality is uneven.
How to identify the pros and cons of UV LED curing system equipment?
Some customers frequently encounter various problems in the process of using UV LED curing system, typical problems such as:
1) UV LED lamp failure rate is high, and the claimed life is seriously inconsistent, some even use less than a few months on a large number of chip damage;
2) UV LED lamp irradiation intensity is insufficient, ink curing degree is low;
There are a variety of causes, but they can be judged from the following three basic aspects:
l Heat transfer - heat dissipation system
LED electrical parameters, life and working temperature are closely related. Usually LED work core junction temperature should be less than 120 degrees Celsius, based on room temperature, every 10 degrees Celsius temperature increase, LED life reduced by 10%. LED packaging and integration in many links need welding, due to the material matching reasons, welding place to bear the thermal cycle stress impact of the material, the greater the temperature change, the greater the stress impact, is an important cause of LED failure. Therefore, the packaging of LED should try to use materials with matching expansion coefficient to minimize heat transfer, and at the same time, high thermal conductivity materials should be used to reduce thermal resistance.
CoolUV all products all adopt the COB (chip on board) packaging, LED chip and the substrate adopts eutectic welding method, welding and substrate using high thermal conductivity aluminum nitride substrate, the thermal resistance of ultra-low, did the shortest chain of thermal conductivity, the minimum thermal resistance, and exclusive technology to ensure the best material matching, to ensure the high reliability of the product, Long service life.
l Power supply -- drive system
LED drive power is DC, so the first thing to change the AC into DC, so need to install ac-DC power supply. High quality AC-DC power supply should have long life, high stability, high reliability, high efficiency, high power factor and other characteristics. Therefore, LED drive is the most important link, which kind of drive, also directly related to the stability of UV LED lamp, life, light efficiency, ease of use, etc..
Traditional constant-voltage and constant-current power supply in the actual use of a large number of chip burning problem, which is related to the LED chip volt-ampere characteristics and the performance of the power supply, the traditional constant-voltage and constant-current power supply design, will lead to instantaneous overcurrent in each circuit power, each load adjustment process, easy to lead to overcurrent damage chip; And LED chip in the operation process, in the whole life cycle, its electrical performance is not fixed, that is to say, even in the packaging of the chip electrical consistency screening, in the operation of the chip will also appear consistency differences; Even if the traditional constant current control is used, the current of individual chips in a large number of arrays will be out of control and damaged.
CoolUV carefully developed special controller, is the crystallization of digital power electronics technology, with powerful and rich functions:
1) For different applications, can be divided into linear constant-current control and PWM constant-current control two driving modes;
2) All can achieve 1% stepless current regulation, high precision, quick adjustment response time;
3) Can realize the millisecond level of fast switching, non-destructive light source life;
4) Advanced CoolUV controller can improve curing degree by 30-50% or more;
5) Real-time monitoring of almost all system states such as temperature, module current and voltage;
6) Rich interface, can support a variety of host computers, and easy to expand.
Although the characteristics of UV LED is fast switching, but the way of switching is very exquisite. The simplest way is to control the LED lights by switching the AC-DC power supply. Or in the DC circuit with a relay control LED lamp. This approach will bring many problems: such as UV LED light response delay, instantaneous current is too large, easy to lead to application problems and lamp failure.
l Optical design
Optical design is an important factor to ensure the intensity and uniformity of UV radiation. Because LED chips are small, most are about 1 square millimeter. Numerous LED package arrays, or COB chip arrays, do not directly bring sufficient radiation intensity and uniformity. When we see that the vast majority of products on the market have no optical design, or only coarse optical design, it is no wonder why these products cure so poorly.
CoolUV r&d team has rich experience in optical design for LED chips. Through precise modeling of chip structure and optical structure, the monte Carlo algorithm is used to simulate the photon movement. The error between the calculated results and the actual measurement is usually less than 5%. In several or even dozens of design schemes through continuous iterative calculation, finally get the matching application of the optimization scheme; With the exception of a few special-purpose products, the vast majority of CoolUV products use only one optical design to achieve excellent performance, which is 20-50% more efficient than solutions that use two or more optical designs.
CoolUV products have different optical designs to suit different applications. The advantages over products with no optical design, simple or even wrong optical design are as follows:
1) Customize the best product solutions according to different application requirements;
2) Use the least energy consumption to achieve the best design objectives, such as high irradiance, high uniformity, collimation light, etc.;
3) Use the minimum number of chips to achieve the same design index;
4) Avoid human design errors or neglect, such as the use of classical optical design
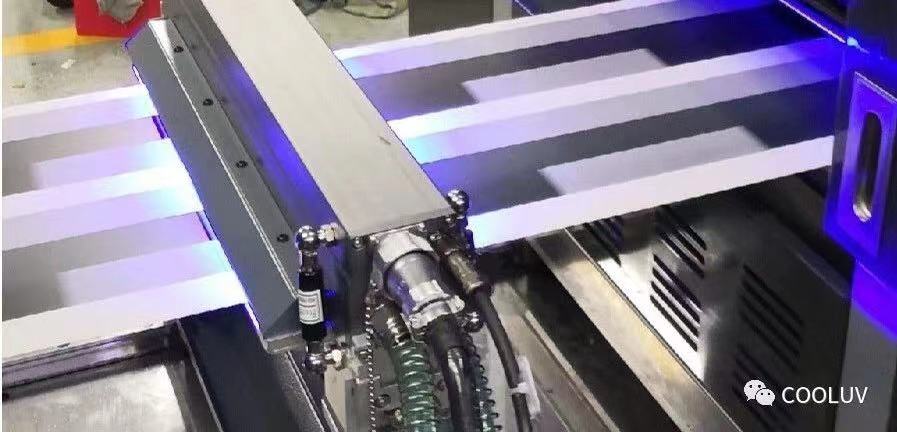
CoolUV facilitates low-carbon and green production in the printing industry
CoolUV SuperCure series products have been widely used in the printing field. Characterized by "green production, energy saving and emission reduction", THE UV LED light curing technology has helped many enterprises around the world to achieve technological upgrading and technological transformation in line with the needs of The Times, resulting in huge economic and social benefits. CoolUV helps the printing industry to achieve low-carbon green production!methods to avoid mistakes.